Types and installation of sheating
OSB is a structural panel made from wood strands that are bonded together under heat and pressure with a waterproof, phenolic adhesive. The strands in the outer faces are oriented along the longitudinal axis of the panel, giving added strength and rigidity in the long direction. The panels are manufactured in sheets 1.2 m (4 ft.) wide and usually 2.4 m (8 ft.) long. The O-1 or O-2 designation indicates an oriented panel, while an R1 designation indicates a panel containing randomly arranged wafers (waferboard). It must be at least 7.9 mm (5⁄16 in.) thick for studs up to 600 mm (24 in.) on centre and 6.35 mm (1⁄4 in.) for studs up to 400 mm (16 in.) on centre. OSB is often identified with a panel mark rating rather than a thickness. When using rated OSB, the panel mark rating must correspond to the stud spacing.
Plywood and OSB wall sheathing are usually applied vertically and are often nailed to the wall framework before a wall is lifted into position. This helps maintain squareness, avoids the need for scaffolding, and speeds construction. Window openings may be covered by the sheathing panels that are cut when window installation occurs. When sheathing is applied horizontally, vertical joints should be staggered.
There are two methods of installing sheathing down to the foundation sill so that it covers not only the walls, but the joist header space as well. One way is to extend the low end of the sheathing panel beyond the bottom wall plate and adding a filler piece at the top. Another way is to use longer 2.74 m (9 ft.) sheathing panels that cover the wall down to the sill area. It is better to cover the header and sill with the same wall sheet because this reduces air infiltration, and when structural panels are in place, it ties the framing to the sill plates.
Leave a 2 to 3 mm (1⁄8 in.) wide space between the sheets to permit expansion. Nail the sheathing panels to the framing with nails spaced not more than 150 mm (6 in.) on centre along the edges and 300 mm (12 in.) along the intermediate supports (Figure 107).
Figure 107

Plywood is a structural panel made from wood veneers that are glued together so that the grain direction of each layer is perpendicular to the adjacent layers. The grain direction of the top and bottom surfaces is parallel to the length of the panel. Sheathing grade plywood is made with waterproof adhesive, unsanded, and may contain knots. The minimum thickness for exterior plywood wall sheathing is 7.5 mm (5⁄16 in.) for studs 600 mm (24 in.) on centre, and 6 mm (1⁄4 in.) for studs up to 400 mm (16 in.) on centre. Sheets are made 1.22 m (4 ft.) wide and usually 2.44 m (8 ft.) or 2.74 m (9 ft.) long.
Fibreboard sheathing should be at least 11.1 mm (7⁄16 in.) thick for studs 600 mm (24 in.) on centre and 9.5 mm (3⁄8 in.) for studs 400 mm (16 in.) on centre. It is made in sheets 1.22 m (4 ft.) wide and generally 2.44 m (8 ft.) long, and is usually impregnated with an asphalt material to increase water resistance.
Gypsum board sheathing consists of a gypsum filler faced on both sides with treated paper or a fibreglass matt facer. It should be at least 12.7 mm (1⁄2 in.) thick for studs 600 mm (24 in.) on centre and 9.5 mm (3⁄8 in.) thick for studs 400 mm (16 in.) on centre. It is made in sheets 1.22 m (4 ft.) wide and 2.44 m (8 ft.) long. The sheets are applied horizontally across the studs and nailed to the framing members.
Insulating sheathing is non-structural. One type is a semi-rigid, glass-fibre panel with an exterior vapour-permeable, waterproof membrane. Another type is made of mineral fibre and has no membrane. Other types of rigid panels are made of expanded polystyrene, extruded polystyrene, polyurethane, isocyanurate or phenolic material. They are available in different thicknesses, and the insulating value per unit thickness varies. Rigid glass fibre sheathing with a vapour-permeable membrane can serve as an air barrier when the joints are sealed with sheathing tape.
Lumber sheathing, which should not be less than 17 mm (11⁄16 in.) thick, is used in boards 140 to 286 mm (6 to 12 in. nominal) wide. It is milled in a shiplap, tongue-and-groove or square-edge pattern. The boards are nailed at each stud with two nails for 140 to 184 mm (6 to 8 in.) widths and three for 235 to 286 mm (10 to 12 in.) widths. Longer nails are required in areas susceptible to extreme wind or earthquake forces.
End joints in the board must be placed over the centre of the studs with the joints staggered on different studs. Lumber sheathing may be applied either horizontally or diagonally (Figure 108) and is extended beyond the subfloor to cover the header joist and the sill plate. The angle cuts of the diagonal approach require more time and materials.
Figure 108
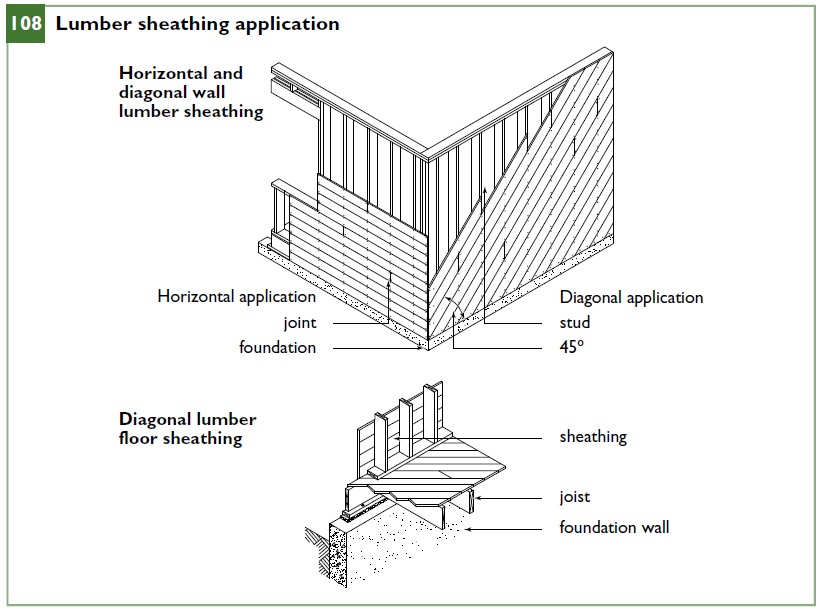
Oncodes.ca publishes this information for educational purposes only (CMHC)
Note: The most common sheating will be OSB and plywood.